solidworks flow simulation heat transfer
For thermal heat transfer analysis choose SOLIDWORKS Flow Simulation over the Thermal solver in Simulation Professional Part 1 of 3 Conduction. Conduction convection and radiation.
Aerodynamics Simulation Virtual Wind Tunnel Using Simscale Aerodynamics Aerodynamics Design Computational Fluid Dynamics
I am doing this in order to see how long it takes for other parts of the assembly to.
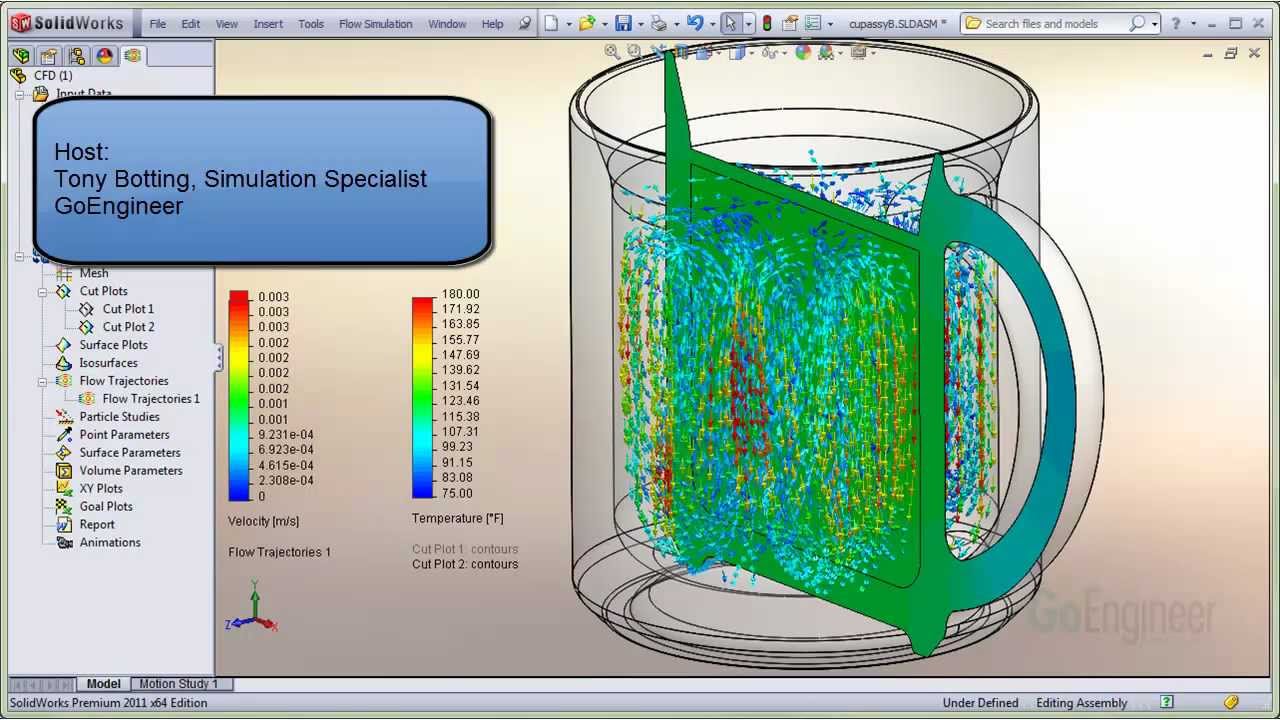
. Heat Transfer Analysis Calculate heat flow in. As you may already know there are three modes of heat transfer. The main 3 reasons why Flow Simulation is the better option will be outlined in a series of three parts.
Learn about developing an animation of heat transfer vs. LM By Lukas Müller 022116. SOLIDWORKS Flow simulation enables true concurrent engineering and brings the critical impact of fluid flow analysis and heat transfer into your workflow to.
Time in SolidWorks Flow Simulation. LM By Lukas Müller 022116. Heat Transfer Analysis Calculate heat flow in.
Once we click the green check the heat source is added. While the software is capable of analyzing a variety of solid bodies and fluid configurations the solutions are typically characterized by flow in or around stationary solid. SOLIDWORKS Flow Simulation - Animation of Time-dependent Heat.
SOLIDWORKS Flow is a general-purpose fluid flow and heat transfer simulation tool integrated with SOLIDWORKS 3D CAD. You can use this CFD solution to simulate both low-speed and supersonic flows. With the exception of very few scenarios when considering a thermal analysis solver for SOLIDWORKS you should choose to use Flow Simulation which is a computational fluid dynamics CFD code.
The ability to simulate heat transfer in fluids is maintained so heat generating solids will automatically convect heat away to the surrounding fluid. SOLIDWORKS Flow Simulation Flux Plot is a result type new in the 2019 version release. QuickTips video presented by Tony Botting of GoEngineer.
More than 25 million product designers and engineers worldwide representing more than 200000 organizations use SOLIDWORKS to bring their designs to life-from the coolest gadgets to innovations that deliver a better tomorrow. Basically I want to heat the top of the component at 210 C and then allow heat to flow through the component and then radiate to the external atmosphere say at 25 C. Conjugate heat transfer through convection conduction and radiation can be created.
SOLIDWORKS Flow Simulation can evaluate the fluid flow for various engineering applications and can facilitate thermal analysis for solving various heat transfer problems. After the simulation is finished I can get the values for the heat transfer coefficient. SOLIDWORKS Flow Simulation allows for the simulation of steady-state and transient heat transfer problems.
With the full SOLIDWORKS Flow Simulation product you have the following advanced functionality. With the exception of very few scenarios when considering a thermal analysis solver for SOLIDWORKS you should choose to use Flow Simulation which is a computational fluid dynamics CFD code. SOLIDWORKS Flow Simulation uses computational fluid dynamics CFD to predict airflow temperature and heat transfer in components boards even complete productseffectively preventing overheating scenarios from occurring.
Hi all I like to simulate the heat transfer coefficient for a specific flow simulation problem. For thermal heat transfer analysis choose SOLIDWORKS Flow Simulation over the Thermal solver in Simulation Professional Part 2 of 3 Conjugate Heat Transfer. Watch how SOLIDWORKS Simulation enables you to evaluate steady-state thermal performance and heat analysis over time.
In this tutorial We will learn how to Do heat transfer analysis in solidworks flow simulation. For our heat source we can specify either a Heat Transfer Rate or a Heat Flux Well choose Heat Transfer Rate and enter 1000 watts for the value. Enabling the radiation option in the Project Wizard allows definition of emissivity and performs simulation of radiative heat transfer.
Calculate pure heat conduction in solids to identify problems where no fluid exists for fast solutions. SOLIDWORKS Flow Heat Transfer SOLIDWORKS Flow Simulation can improve design productivity and may dramatically reduce the number of physical prototypes needed for testing. I have an assembly in Solidworks 2010 and I am trying to simulate heat transfer throughout the component using the Simulation tool.
With the full SOLIDWORKS Flow Simulation product you have the following advanced functionality. We will mix hot and cold water in soliworks flow simulation t. Calculations can include thermal contact resistance.
Air or liquid flow is a critical part of keeping any electronics properly cooled this video shows how Flow Simulation handles both aspects of such problems. Solidworks flow simulation heat transfer may 22nd 2020 - solidworks flow simulation allows for changes to the design and analysis to be cycled through at the same time and it shouldn t be too long before an improved cold plate is nailed down i hope you. It allows for the display of heat flux results between model components and project features as a network chart.
I dont define any temperatures nor any heat flows. Simulate heat transfer coefficient. If we zoom out we can see the total project setup the three boundary conditions and the heat source along with their current values displayed in the flags.
Flow Simulation Project Wizard. SOLIDWORKS Simulation will calculate conduction but it is up to us to define the parameters for convection and radiation. SOLIDWORKS Flow Simulation HVAC Module can fully assess the thermal environment created by heating and cooling systems With an easy-to-use fluid-flow analysis application like SOLIDWORKS Flow Simulation software you will have the tools that you need to solve even the most difficult heat transfer problems while saving time and money in the process.
Equally important it encourages engineers to explore many more. This question has a validated answer. The heat flux output will display the amount of heat transfer from one component to another through conduction.
Transient Flow Analysis In Solidworks Flow Simulation Solidworks Analysis Flow Training
Pin On Computational Fluid Dynamics Cfd
Flow Simulation Heat Exchanger
Solidworks Flow Simulation Transient Manifold Airflow Industrial Design Sketch Solidworks Solidworks Tutorial
Suction Pump Simulation Using Flow Simulation Solidworks Tutorial Solidworks Simulation
Solidworks Flow Simulation With Fan And Heat Hink Solidworks Solidworks Tutorial Futuristic Background
Solidworks 2011 Tutorials Flow Modelling Simulation Of Airfoil Part 2 Of 2 Solidworks Airfoil Tutorial
Cfd Analysis Of Multiphase Flow Analysis Services With Cfd Consulting Services Consulting Oils Analysis
An Image Of Aerodynamic Analysis Of A Vehicle Wing Mirror That Shows The Pressure Distribution Of Mirror Surface And Velocity Distribution
We Offer Heat Transfer Analysis Services To A Large Range Of Industrial And Manufacturing Co Computational Fluid Dynamics Environmental Analysis Cfd Simulation
Easily Simulate Fluid Flow Heat Transfer And Fluid Forces That Are Critical To The Success Of Your Design With Solidworks Flow Simulation Contact 91 Scherma
Solidworks Flow Simulation Transient Natural Convection Solidworks Simulation Flow Training
Introduction To Solidworks Flow Simulation Solidworks Mechanical Design Simulation
With Its Cfd Analysis Capabilities You Can Simulate Liquid And Gas Flow In Real World Conditions Run What If Sc Computational Fluid Dynamics Fluid Flow Fluid
Turbulent Flow Through A Cyclone Separator Https Www Simscale Com Projects Dheiny Turbulent Computational Fluid Dynamics Engineering Projects Fluid Dynamics
Solidworks Static Analysis Two Bar Assembly Analysis In 2022 Solidworks Structural Analysis Analysis